Plastic Bauer rings in the pharmaceutical industry
Release time:2025-03-31
Release time:2025-03-31
At the core of the pharmaceutical industry, the innovation of separation and purification technology is always the key to improving product quality and production efficiency. As a new type of filler, the plastic Bauer ring, with its unique structural design and material properties, is gradually penetrating many areas of the pharmaceutical industry, for the traditional process to bring optimization space.
I. Structural characteristics and material advantages
The design of a plastic Bauer ring breaks through the limitations of traditional filler. The uniform distribution of the ring wall window structure (usually 30%-50% of the ring wall area), allows the gas and liquid phases in the packing layer to form a three-dimensional flow path, which significantly improves the mass transfer efficiency. For example, the use of polypropylene Bauer rings in the absorption tower of a fluoride salt plant resulted in an increase in fluoride uptake of about 40% and a 30% reduction in power consumption. Compared with ceramic or metal filler, the density of plastic material is lower (such as polypropylene density of about 0.9g/cm³), which can reduce the load on the equipment, and at the same time, its chemical stability (acid and alkali resistance of more than 99%) to meet the pharmaceutical industry's demanding requirements for corrosive environments.
II.Typical Application Scenarios
Solvent recovery system
In the production of pharmaceutical intermediates, plastic Bauer rings are widely used in solvent distillation columns. Its high porosity (up to 95%) and low-pressure drop characteristics can achieve higher efficiency recovery of organic solvents such as ethanol and acetone. By using polypropylene Bauer rings in a reduced-pressure distillation column, a pharmaceutical company was able to increase solvent recovery from 85% to 92% and reduce energy consumption by 15%.
Wastewater Treatment
Pharmaceutical wastewater often contains high concentrations of organic matter and heavy metal ions. Plastic Bauer rings are used as fillers in biofilters, and their surface roughness (Ra value of 3.2-6.3 μm) provides an ideal attachment carrier for microorganisms. After the introduction of PVC Bauer rings into the wastewater treatment system of an antibiotic manufacturer, the COD removal rate was stable at more than 85%, and the packing life was extended to more than 5 years.
Reaction towers and catalytic carriers
Plastic Bauer rings can be used as catalyst carriers in continuous reaction processes. For example, in the synthesis of ibuprofen, PTFE Bauer rings loaded with metal catalysts can increase the reaction conversion by 10% and simplify the product separation process.
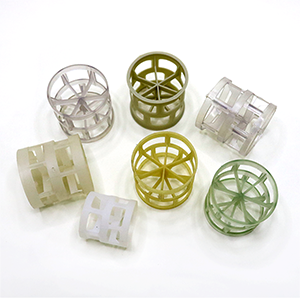
III. Industry Trends and Technological Innovation
Material upgrading direction
The application of new modified materials such as PPH (β-crystalline polypropylene) has improved the temperature resistance of plastic Bauer rings to 120°C, which can meet the needs of high-temperature distillation processes. Meanwhile, the development of polyvinylidene fluoride (PVDF) has further expanded its applicability in strong oxidizing environments.
Intelligent Production Adaptation
As the pharmaceutical industry transforms into continuous and intelligent production, the modular design of plastic Bauer rings (e.g., combined packing tower internals) can be seamlessly adapted to automated control systems. A biopharmaceutical company introduced an intelligent monitoring system to adjust the gas-liquid ratio of the packed layer in real-time, resulting in a 20% increase in purification efficiency.
Environment and Sustainability
The requirement for recycled plastic content in the EU ELV Directive (to be implemented in 2025) has driven the development of recycled plastic Bauer rings. Fillers produced using chemically recycled technology have comparable performance to virgin materials and a carbon footprint that is more than 30% lower.
IV.Challenges and Strategies
High Temperature and High-Pressure Scenario Limitations
The mechanical strength of plastic Bauer rings (compressive strength of approx. 6-10 N/mm²) is still inferior to that of metal fillers in processes where high temperatures of over 200°C or pressures of over 10 MPa are required. Solutions include the development of fiber composites or hybrid filler structures.
Biocompatibility verification
When used in aseptic manufacturing environments, plastic Bowls need to pass USP Class VI biocompatibility testing. Companies can work with material suppliers to customize specialized fillers to meet pharmaceutical standards.
Conclusion
Plastic Bauer rings are reshaping separation and purification processes in the pharmaceutical industry with their structural innovations and material advantages. With the integration of materials science and intelligent manufacturing technology, its application scenarios will be further expanded. When choosing fillers, companies need to consider process needs, cost-effectiveness, and environmental requirements, and achieve continuous improvement in production efficiency through technology iteration. In the future, with the global emphasis on sustainable development, recyclable plastic Bauer rings are expected to become the mainstream choice for the industry, providing support for the green transformation of the pharmaceutical industry.
RELATED INFORMATION

Customer Service Hotline
Tel/WeChat/WhatsApp:+8618079942828
E-mail/Zoom:jlee@pxrjhb.cn
Address: No. 1-269, Zone B, Industrial Park, Xiangdong District, Pingxiang City, Jiangxi Province

Website construction:300.cn