Optimised design of metal Bauer rings for pharmaceutical applications
Release time:2025-03-31
Release time:2025-03-31
INTRODUCTION
In the core production process of the pharmaceutical industry, the efficiency of the separation and purification process directly affects the quality of the drug and the production cost. As the core component of the packed tower, the performance optimization of the metal Ball ring becomes the key to improving the process level. In recent years, through material innovation and structural design breakthroughs, metal Bauer rings have made significant progress in mass transfer efficiency, corrosion resistance, and operational stability, providing important support for the green and intelligent transformation of the pharmaceutical industry.
I,structural design optimization: from foundation to innovation
The structural design of the traditional metal abalone ring is based on the Lacy ring, which improves gas-liquid distribution by opening window holes in the ring wall. In recent years, researchers have further optimized the layout of the window holes and the shape of the blades. For example, **Hy-PaK** has changed the inward curved blades of each window hole from a single blade to a double blade with the top and bottom reversed, and at the same time pressed a convex rib on the ring wall. This improvement increases the number of mass transfer points inside the packing by 30%, and significantly improves the efficiency of liquid droplet formation and film renewal, increasing the mass transfer rate by more than 10%. Additionally, the ribbed structure increases the strength of the ring wall, allowing for thinner wall thicknesses and reducing the load on the supporting structure of the packed tower.
In terms of size design, the enterprise developed DN50*0.8 specification metal Bauer ring for the special needs of the pharmaceutical industry. Its ring structure and window distribution have been optimized by hydrodynamic simulation, and it shows a lower pressure drop (about 50% lower than the traditional Bauer ring) and higher flux (more than 10% increase in processing capacity) in vacuum distillation and other scenarios. This design is especially suitable for the treatment of heat-sensitive pharmaceutical ingredients, which can effectively avoid the destruction of drug activity by high temperatures.
II, material innovation: to meet the challenges of complex working conditions
Pharmaceutical production, corrosive media, and high-temperature environments put forward stringent requirements for packing materials. Metal Ball ring material selection from a single stainless steel to diversified, high-performance direction:
Corrosion-resistant alloys: 316L stainless steel contains molybdenum elements, in the acidic medium shows excellent resistance to pitting corrosion, widely used in antibiotic production in the extraction tower. Duplex steel 2205 (22Cr-5Ni-3Mo-N) has both austenitic and ferritic advantages, its strength is twice as strong as 316L, its corrosion resistance is better, and it is suitable for high concentrations of acid and alkali environments.
Specialty metals: Titanium alloy Bauer rings are emerging in the biopharmaceutical field, with their low density, high strength, and good biocompatibility, avoiding contamination of drugs by metal ions. For example, in the purification process of vaccine production, titanium fillers can effectively prevent residual metal impurities from affecting product purity.
Surface treatment technology: Through chemical coating or electrochemical polishing, the surface roughness of metal Bauer rings is reduced, reducing the risk of liquid retention and scaling. An enterprise adopts nano-ceramic coating technology, so that the filler's wear-resistant performance increased by 3 times, prolonging the service life.
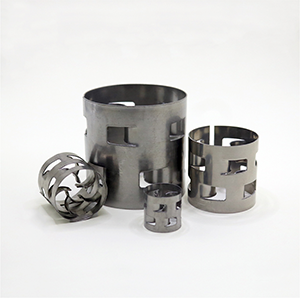
III, the manufacturing process upgrade: from traditional to intelligent
To meet the requirements of the pharmaceutical industry for high precision and consistency, the manufacturing process of metal Ball rings is accelerating the intelligent transformation:
Automated production: Jiangxi Aite mass transfer technology introduced multi-slider latent glue mouth automatic mold, to achieve the whole process of Bauer ring production automation. The daily capacity of one production line has increased from 2 m3 to 20 m3, and labor costs have been reduced by 16%.
Digital factory: Pingxiang Dier Chemical established the first digital factory in the mass transfer material industry, realising real-time tracking and quality tracing of the production process through AGV handling, remote AR monitoring and other technologies. Digital management has reduced the defective rate from 5% to less than 1%.
Precision machining: The application of CNC machining equipment ensures the high precision of packing dimensions. For example, the tolerance of inner and outer diameters of DN100 stainless steel Ball ring is controlled within ±0.1mm, which improves the uniformity and mass transfer efficiency of the packing layer.
IV,typical applications and industry impact
The optimized design of metallic Bauer rings has shown significant benefits in the pharmaceutical sector:
Vacuum distillation: In the production of vitamin C, the application of Haepack packing reduces the pressure drop of the distillation column by 40%, reduces the unit energy consumption by 15%, and improves the purity of the product from 98.5% to 99.2%.
Bio-pharmaceuticals: a monoclonal antibody drug manufacturer used titanium alloy Bauer ring, in the purification process to improve the impurity removal rate to 99.9%, while avoiding the traditional stainless steel packing that may introduce metal ion pollution.
Environmental upgrade: In pharmaceutical wastewater treatment, 316L stainless steel Bauer rings are used in decarburisation towers, where their corrosion resistance and high flux characteristics improve system stability and reduce equipment maintenance frequency.
Industry data shows that the optimised design of metal Bauer rings has reduced unit energy consumption in the pharmaceutical industry by about 8-12%, and shortened the equipment payback period to 2-3 years. With the global requirements for quality and sustainable production of drugs continue to improve, the market demand for high-performance metal Ball ring is expected to grow at an average annual rate of 7%.
V,future Trends and Challenges
Although significant progress has been made in the optimization of metallic Bauer rings, the industry still faces the following challenges:
Adaptability to complex operating conditions: For extreme temperatures (e.g. - 200 ℃ deep cold or 300 ℃ high temperature) and strong oxidizing media (e.g. hydrogen peroxide), new alloy materials need to be further developed.
Intelligent monitoring: the combination of the Internet and sensor technology to achieve real-time monitoring of filler performance and early warning is a key direction for future research.
Cost control: high-performance materials and manufacturing process costs are high, and need to reduce the application threshold through large-scale production and technological innovation.
Conclusion
The optimal design of metal Bauer ring is the epitome of the pharmaceutical industry's technological upgrading. Through structural innovation, material breakthroughs and intelligent manufacturing, metal Bauer rings are driving pharmaceutical production in the direction of high efficiency, green and intelligent. With the integration of interdisciplinary technologies, metal Bauer rings will show their potential in more segments in the future, providing strong support for the sustainable development of the global pharmaceutical industry.
RELATED INFORMATION

Customer Service Hotline
Tel/WeChat/WhatsApp:+8618079942828
E-mail/Zoom:jlee@pxrjhb.cn
Address: No. 1-269, Zone B, Industrial Park, Xiangdong District, Pingxiang City, Jiangxi Province

Website construction:300.cn